What to do if the puncher has ceased to hammer out smoothly
If the puncher has stopped hammering, it is necessary to evaluate the expediency of the repair. Imitations of popular brands, cheap modifications to restore meaningless - they are not designed for a long resource, the cost of repair is approaching the purchase of a new power tool. Models of famous brands last longer, their replacement is often caused by the appearance of modifications with additional features and obsolescence.

Figure 1. Device punch.
The lack of prevention after 100-80 hours of work will inevitably lead to the failure of the punch.
Punch malfunctions
After the tool has stopped working, many users try to eliminate the cause on their own to save time. It is strongly not recommended to do this, since the industry produces several types of perforators:
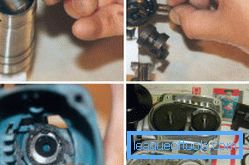
Figure 2. Lubrication Perforator Stages.
- electromagnetic - the peak in them beats due to the reciprocating motion of the core inside the coils;
- electropneumatic - the clutch assembly transmits a blow through the air cushion to the flying piston through the impact piston.
The impact energy in the second case is five times larger, reaching 1.5 kW. In the broken shanks of parts, fatigue failures begin with time, therefore, despite the air cushion, the pistons require periodic replacement. Fig. one
There are straight, L-shaped tool bodies. The first are intended for limited spaces (niches, narrow slits), the second - for the destruction of materials in the immediate vicinity of the working body. The cooling of the engines of the L-shaped models is much more efficient, so their life exceeds the direct modifications by one and a half times. Professional rotary hammers are equipped with powerful electric motors, often have an L-shaped case, much heavier than domestic counterparts. Compensators are installed in them that reduce vibrations on the tool body, electronic systems for protection against overheating, speed adjustments (for drilling mode), improved ventilation systems, button locks.
Back to table of contentsCauses of perforator breakage

The principle of operation of the percussion hammer mechanism.
If the puncher has stopped working, the reasons may be as follows:
- malfunction crank mechanism;
- development of the intermediate shaft;
- lack of lubrication;
- worn clamping unit;
- mechanical damage to the percussion elements (face or clutch).
The perforator must be periodically lubricated by applying special material instead of traditional Litol. Savings on tooling leads to intensive wear of the barrel, which houses the bit / bit shank. Fig. 2
The perforator does not beat after a significant amount of lubricant flows out of the gearbox when the glands and rings are worn. Rubber parts work in aggressive environments, extreme conditions. With a significant accumulation of dust and crumbs on their surface, the material loses elasticity, bursts, cracks from loads.

Diagram of the device components of the punch.
Violation of operating modes is dangerous for a punch:
- inexperienced users unduly put pressure on the hull in the bump stop mode, forgetting that the chisel works due to the effort of the internal mechanism, the amplitude of the striker stroke decreases, leading to its breakage;
- a change in the bit trajectory with some penetration of the working body into the material being destroyed leads to wear of the piston, striker, bearings, and the crank assembly;
- overheating of the tool during prolonged use in difficult conditions is fraught with a cut of the teeth of gears.
A hammer drill is often used to shave ceilings, which increases the amount of dust in the spindle. External anthers are not able to protect the internal components from the penetration of abrasive. Internal anthers are equipped with tools from two or three manufacturers (for example, the Kress PK450HM model), therefore periodic revision and cleaning of the clamping unit is required.
Strong noise in the gearbox indicates the wear of the gears or the breakdown of the teeth, excessive heating of this unit prevents either the absence of oil or the deterioration of bearings.
The power tool can work in the drilling mode without a bump stop, but not vice versa. When the node of rotation is damaged, the slotting becomes impossible, since the internal mechanisms are jammed. In this case, urgent repairs will cost ½ - of the cost of a new tool, which is economically unprofitable for the user.
Back to table of contentsTroubleshooting Methods

Scheme of removal of the lever.
Self repair punch is extremely difficult complex structure. Even dismantling the case is often an impossible task for the home wizard.
Specialists of service centers of leading brands, in addition to the corresponding education, have a regular practice of work, the necessary tools and devices.
In addition, the diagnosis of power tools is made at the initial examination, which allows you to plan a budget: invest in an existing tool without guarantees of long-term operation, or spend money on a new power tool with a high resource, manufacturer's warranty.

Punching gear reducer disassembly: 1 - special ring, 2 - release sleeve, 3 - ring, 4 - ball, 5 - spring 8 - casing, 22 - closing spring, 28a - switch, 29 - ring, 30 - spring, 31 - clamp.
The perforator is used in different modes, which significantly reduces the resource of the working bodies. In addition, specialized companies often use either chiseling (concrete, stone work, restoration of buildings, foundations), or drilling (installation of household, industrial equipment). If in the second case, following the manufacturer's recommendations on drilling modes, it is possible to extend the service life of the electric tool, then in the first variant it is very difficult to calculate the load. For example, at the specified maximum drilling rate of 24 mm concrete, it is recommended to use drills in the range of 18-16 mm. Peaks for the destruction of concrete, stone, brick - standard, so the tool is experiencing various loads.
If the power tool stopped beating, you can limit the disassembly of the spindle assembly in the following sequence:
- dismantling of the mode lever - parts are usually made of polymers, therefore they are quite fragile;
- anther detachment - a rubber corrugation should be periodically replaced, as it often contacts with destructible materials, wears out, cracks;
- when the cartridge is collapsible, brushes are first removed; screws are loosened and loosen;
- the body is divided into two halves.
A visual inspection in 90% of cases allows you to identify a malfunction, replace a damaged / worn part. Before assembly, it is mandatory to add, replace the grease.