How to make a homemade band saw for wood
The self-made tape saw is a functional adaptation, irreplaceable in work of the master in processing of a tree and many household questions. It is quite simple to make such equipment if you make some efforts and strictly adhere to the recommendations.

Circuit band saw.
The design of the equipment includes a desktop, which serves as the basis for the placement of the remaining elements, which are shown in the drawing (Fig. 1). In this image, the numbers from 1 to 16 respectively denote the following structural elements:
- Lower drive pulley.
- Desktop box.
- Saw blade.
- V-belt.
- Vibration damper
- Guide.
- Carrier rod.
- Upper drive pulley.
- Tabletop.
- Electrical engine.
- Belt drive pulleys.
- Mounting bracket.
- Nut.
- Upper support.
- Screw for adjusting the operating mode.
- Slider
Making a desktop
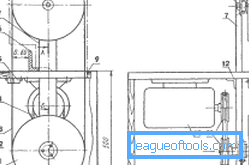
Figure 1. Band saw design (designations in the text).
The recommended material for the manufacture of the working surface of the table and bed - plywood 2 cm thick. You will need a piece of plywood with standard for your desktop band saw parameters - 42x72 cm. From above the plywood is glued with textolite. For edging workpiece under the worktop around the perimeter are used slats from hardwood.
To maintain the band saw wiring, it is necessary to provide grooves in the working surface. As a result, the desktop will be a box that is glued together from plywood of the required thickness. Its dimensions should be 42x72x50 cm. Sawdust will be collected in the inner space of the box.
The bearing bar is attached to the table. For its manufacture, you will need a channel of N 8, 68 cm long. For reasons of convenience, further operation of the band saw shelf on the channel requires cutting to a height of 2 cm. A fixing bracket and 4 bolts are used to fix the rod. Its scheme is presented in fig. 2

Figure 2. Scheme of the rod for band saws.
The same plywood with a thickness of 20 mm is used to grind the belt drive pulleys. Polyurethane glue on the surface of the pulleys glued rubber sheet. After that, the wood is required to impregnate with epoxy. Next, it must be polished and painted. In order for the band saw to be held on the working surface, it needs to be barrel-shaped.
The dural bushing in which the seat for the ball bearing is prepared should be glued into the upper pulley shown in fig. 3, epoxy resin. With the help of 3 5x20 screws, the lower pulley is fixed on the steel axis. The other end of the axle is placed in the bush in which 2 ball bearings are placed. The axle box is mounted on the lower end of the carrier bar. With the aid of a spacer sleeve, the end of the steel axis secures the driven belt drive pulley.
Back to table of contentsBalancing sawband pulleys
Driven and driven pulleys are the same. However, depending on the motor shaft, the mounting hole for the driving pulley is determined.
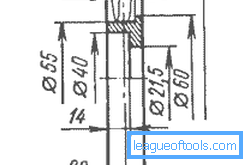
Figure 3. Fastening scheme for dural aluminum bushings.
To eliminate the vibrations of the tape, a special damper is required, as in fig. 4. For its manufacture, textolite parts are used, which are bolted with M6 bolts. This vibration damper is fixed with a fixed part to the bottom surface of the table. Moving bar selects the required clearance.
If necessary, you can install the upper damper. This may be necessary if the upper belt pulley hits the diameter.
Back to table of contentsInstallation guide

Figure 4. Diagram of a special damper.
The timber that will be sawn is fed into the working area using a guide, as in fig. 5. To install it, you will need to make 2 slots on one of the shelves along the edges. They will be used to adjust between the tape and the guide. For the stroke of the strap in the middle of the shelf provides a cutout.
For the manufacture of the rail itself will need a steel corner 100x100. The top pulley assembly is placed in a protective casing to ensure safe working conditions. The tape will not be closed to them only in the work area.
Back to table of contentsSaw tape making
Saw band is the main functional device of the equipment, so its manufacturing requires special attention.
Not every material is suitable for its manufacture.

Figure 5. Installation guide.
On the one hand, the tape is necessary elastic, and on the other - with high strength. The ideal material to achieve such a combination is cold rolled sheet steel. Its optimum thickness is determined by the type of wood that will be cut. For soft rocks, it is acceptable to use steel with a thickness of 0.2-0.4 mm. For solids, thickness from 0.4 mm to 0.8 mm is required.
If the machine is manufactured according to the dimensions given in Figure 1-6, the length of the workpiece will have to be 1.6-1.7 m. When cutting the teeth between them, a distance of 3 mm is preserved. The tape is folded and soldered to loop. Next, the seam of the commissure is sprinkled with brown and heated with a gas torch. The result should be the same as in fig. 6

Figure 6. Scheme of manufacture of a saw tape.
It is possible to impart greater strength to the metal that forces the seam, if it is coated with the solder of the ПСР-40 brand. After that, the place of adhesions is strongly compressed with pliers, using asbestos pads on its working surfaces. After this, the seam of the spikes can be sanded so that the saw is smooth and works without interruption. In order to obtain a high-quality cut, it is further recommended, after sharpening the cut teeth, to arrange them.
According to the above guide with the provided drawings, a band saw for wood can be made by your own hands. The model is slightly simplified, it is ideal for domestic use, however, the departure of its canvas is small. It is possible to eliminate this disadvantage if you make some adjustments to the design and use larger diameter pulleys during the installation of the carrier bar.
Thus, the construction of a band saw with your own hands is a task feasible for practically everyone. The result will be equipment capable of sawing blanks up to 10 cm thick for soft rocks and up to 4 cm for hard ones.
In making the saw, it is necessary to be extremely attentive, since the safety of the master, who will work with wood materials with the help of the device obtained, depends on its strength. It is very important to choose the right materials for effective equipment operation. Only steel of certain brands can serve as a high-quality saw blade. That is why it is necessary to choose it carefully.